We absolutely love these 27″ iMac’s, although they are 2009-2013 models they are so powerful that can last for another 5 years with no doubt.
However like any other iMacs and Mac computer they have a weakness – the heat. When they get clogged with dust and fluff, their cooling system becomes ineffective.
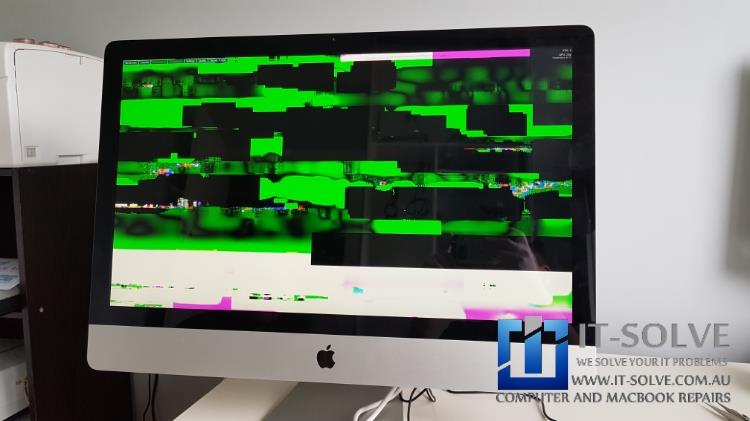
Exactly this happened to our customer. His iMac graphic card failed and he start getting these colorful patches on the screen just before it would turn black and shut down.
He mentioned that his graphic card was replaced recently (couple years ago) by an Apple Authorized Service Center and wanted to understand why it fail in such a short time. He also said that the service center refused to clean his iMac when he saw how it looks inside.
Repair Process
A straight forward option here is to replace the graphic card with a new one. However, due to the popularity of these iMac and seized production of these Graphic Cards they are hard to find on the market.
Hence we try to repair them first by reflowing them with our graphic card repair equipment. This resolves majority of iMac graphic problems by repairing them.
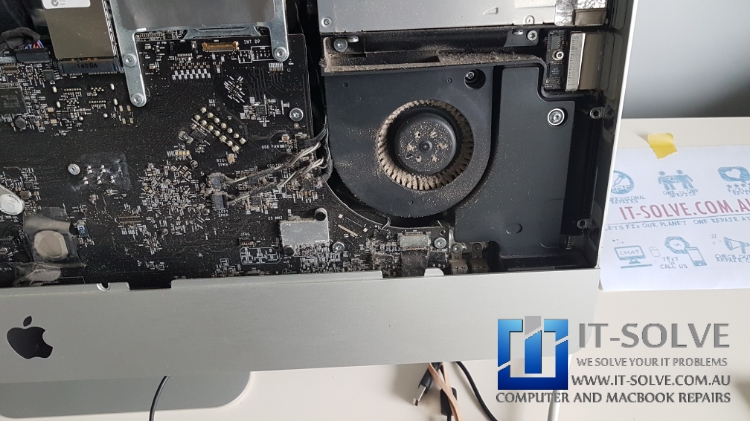
When opened we could see how clogged the fans are, with dust and fluff collected over the years. This is the main reason for the majority of the failures on these iMacs. From hard drive failure to graphic card problems with iMac, heat is the number one enemy of the electronics.
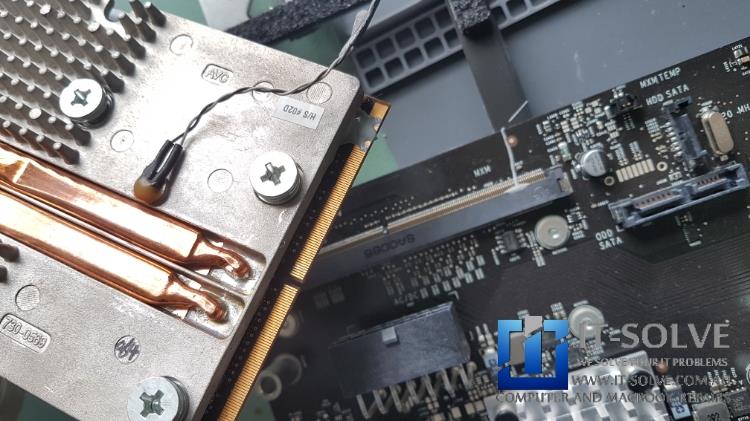
We start taking the logic board out and have noticed something we haven’t seen before. There was a leak of thermal paste over the power socket of the graphic card. Although the viscosity of the thermal paste was quite high, this paste managed to leak all the way to the connectors.
We start wondering how much thermal paste was applied to this graphic chip. Ideally it should not be more than a pea size blob, based on the Intel documentation. The procedure and amount is same for all chips regardless manufacturer, generating heat over 80*C
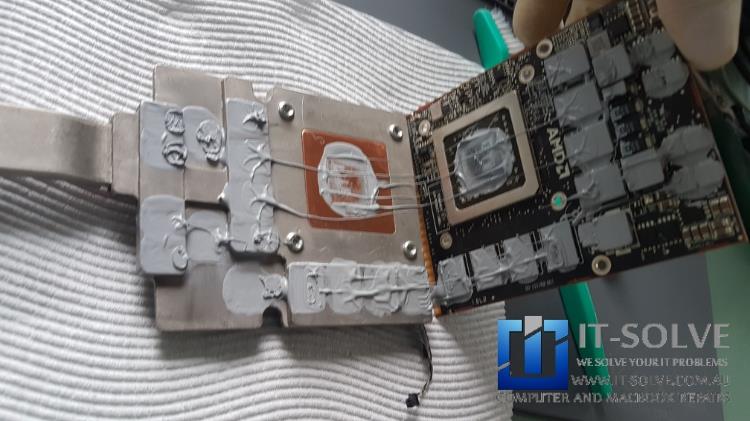
iMac White Screen Repair service we offer here in Adelaide includes a couple of simple steps:
- Get a Quote for the repair before any work is done, even over the phone.
- Free pick up from the client’s location in Adelaide. Or alternatively, drop in for a quick check while you wait.
- Confirming final cost and “Go” from the client.
- Repairing and ensuring everything works as expected.
- Returning repaired system back to the client. Or the client can pick it up from our workshop.
Apparently technicians at this Authorized Repair Center must have ran out of thermal pads and decided best they can do is to cover every chip on the board with a thermal paste to increase heat conductivity.
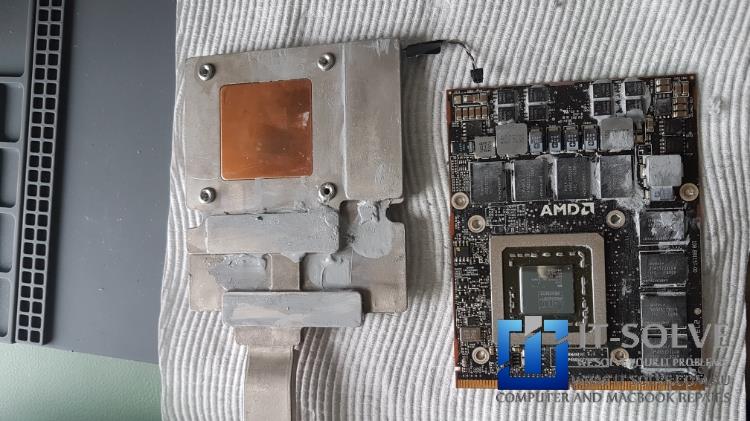
However, the reality is that there is couple millimetres space between the MOSFETS, Memory chips, Coils and the heatsink. And thermal paste is not tick enough to be able to fill the gap. There is only way of filling the gap and it is a thermal pad. These around a millimetre tick and ensure that when heatsink pushes against them, they can shrink and increase thermal conductivity.
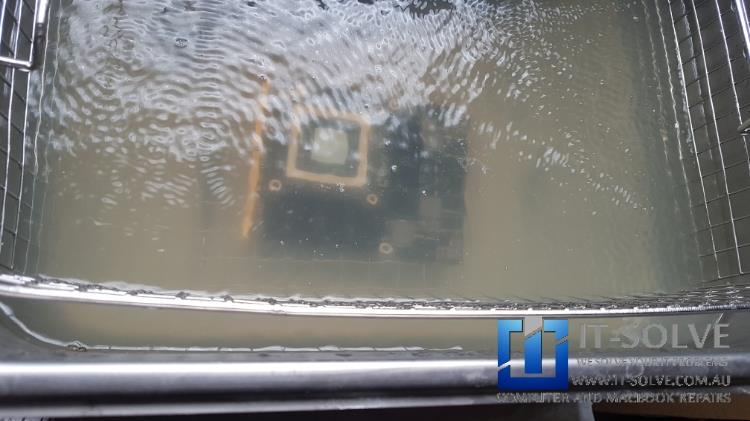
Initially we tried to scrub the silver thermal paste from the chips on the graphic card, but due to the heat its viscosity changed drastically and it slide under memory chips. Although thermal paste has no conductivity properties we would not know how it would respond under heat of above 80*C. We did not wanted to risk it and wanted to clean it.
We had to sacrifice whole batch of PCB cleaner in our ultrasonic bath just to get rid of the thermal paste from underneath the chips.
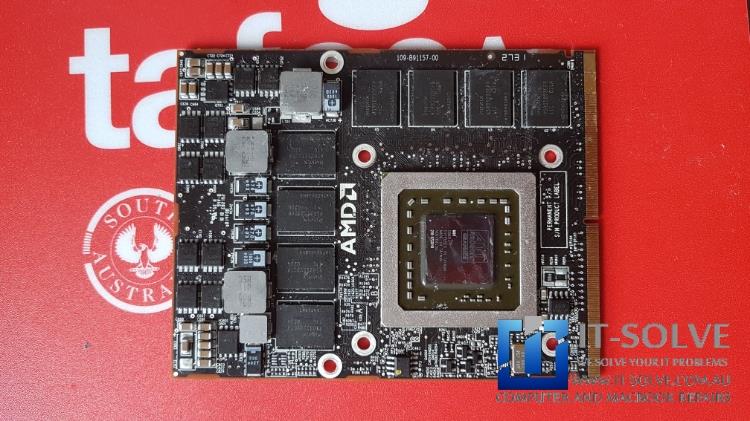
Once Graphic Card was cleaned we were ready for the real deal – iMac Graphic Repair process. We absolutely love this step, as we can play with the heavy machinery. Especially after we recently upgraded our BGA repair and reflow system with more powerful and precise one.
Reflowing the graphic chip requires following a reflow procedure which resolders the chip. It is a complicated procedure and too long to explain here. Feel free to have a chat with our engineers if you would like to understand the process.
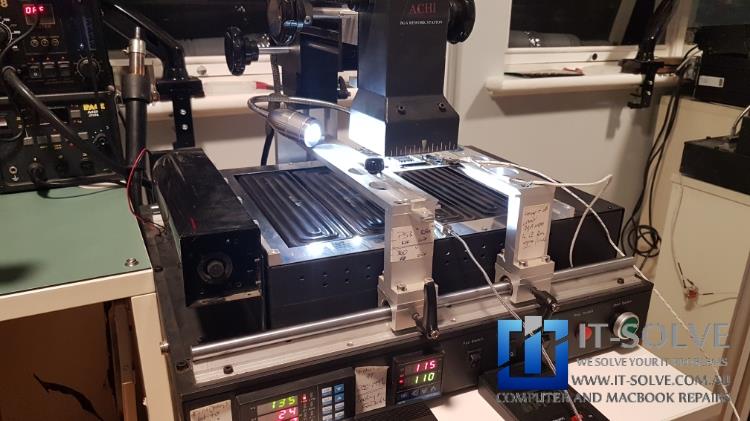
The Result
We wanted to ensure customer is getting best out of this absolutely state of the art iMac. Probably last of its breed.
So we added correct thermal pads and applied just enough amount of thermal paste to spread evenly on top of the graphic chip without overflowing.
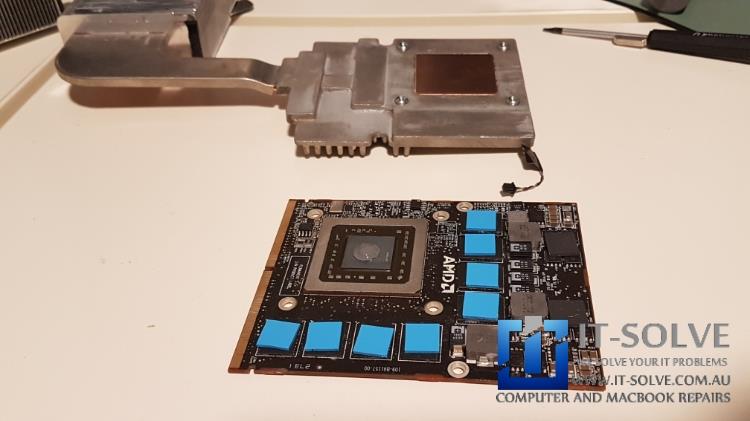
Once the repair was completed, we assembled back the iMac and run overnight heavy graphic tests. Following 12 hour constant video streaming tests. These tests are much heavier than the usual usage of these computers. And if repair is not stable, we would catch issues during these tests.
Interested in similar graphic repairs? Check out some of our published repair cases.
Please note: This is not educational material. It is rather a showcase of the services we offer.
Therefore, it should be used as general guidance on what to expect of such repairs.
In case you have a similar device and need the repair, always rely on professionals. These are sensitive electronic devices, and small mistakes may cause irreversible electronic damage. Which may require whole part replacement for 2 or 3 times the cost.
Do you need iMac Graphic Repair service in Adelaide?
Do you need this Repair in Adelaide?
If your Apple Mac or Macbook is causing trouble and need a Macbook Repair Service in Adelaide, give us a call, and we will advise on the best scenario to get your device repaired.
Interstate? Why not Send IT for a Repair. Repairs take under three weeks, including forward and backward postage. Contact us to get an idea of cost and turnarounds.
We at IT-Solve, specialise in Apple Mac and electronics repairs. We will do our best to repair your Mac quickly without involving high costs and long waiting times in repair shops. Our average repair takes under a week!
Call us now on 0469317177 or drop us an inquiry via WhatsApp or
Messenger
Our engineers will respond quickly to your query.
Repaired, not Replaced!
We are committed to reducing e-waste in Australia. How we do it is by educating our customers on the reparability and longevity of their devices, as well as providing affordable Macbook Repairs here in Adelaide.
Although our best intentions and hard work, this is not an easy task. Customers must accept that cost of high-quality electronic repairs, is between a third and half of the price of a new device. However, with the current trend of planned obsolescence in electronic design, we see more and more Macbooks having shorter lifespans. To tackle that, while we do our repairs we target common planned obsolescence engineering design mistakes to ensure we extend the life expectancy of the Macbooks we repair. Check some of our Macbook Repair Cases to get an idea of the process.
That said, if we buy a new one or write it off via insurance, it does not guarantee that the new one will not meet the same fate as the older one pretty soon.
As matter of fact, quite often we see accidents reoccurring within less than 2-year gaps. If we can save 2000$ or even 1000$ today by repairing our faulty Macbook is brilliant. That’s an extra half Macbook cost ready to be spent on another one when the time comes or our need for performance increases.
When that time comes is up to us to buy a new one or keep pushing the one we have, but delaying it by a year or three is always a good starting point and saves another abandoned Macbook from polluting our one and only Planet.